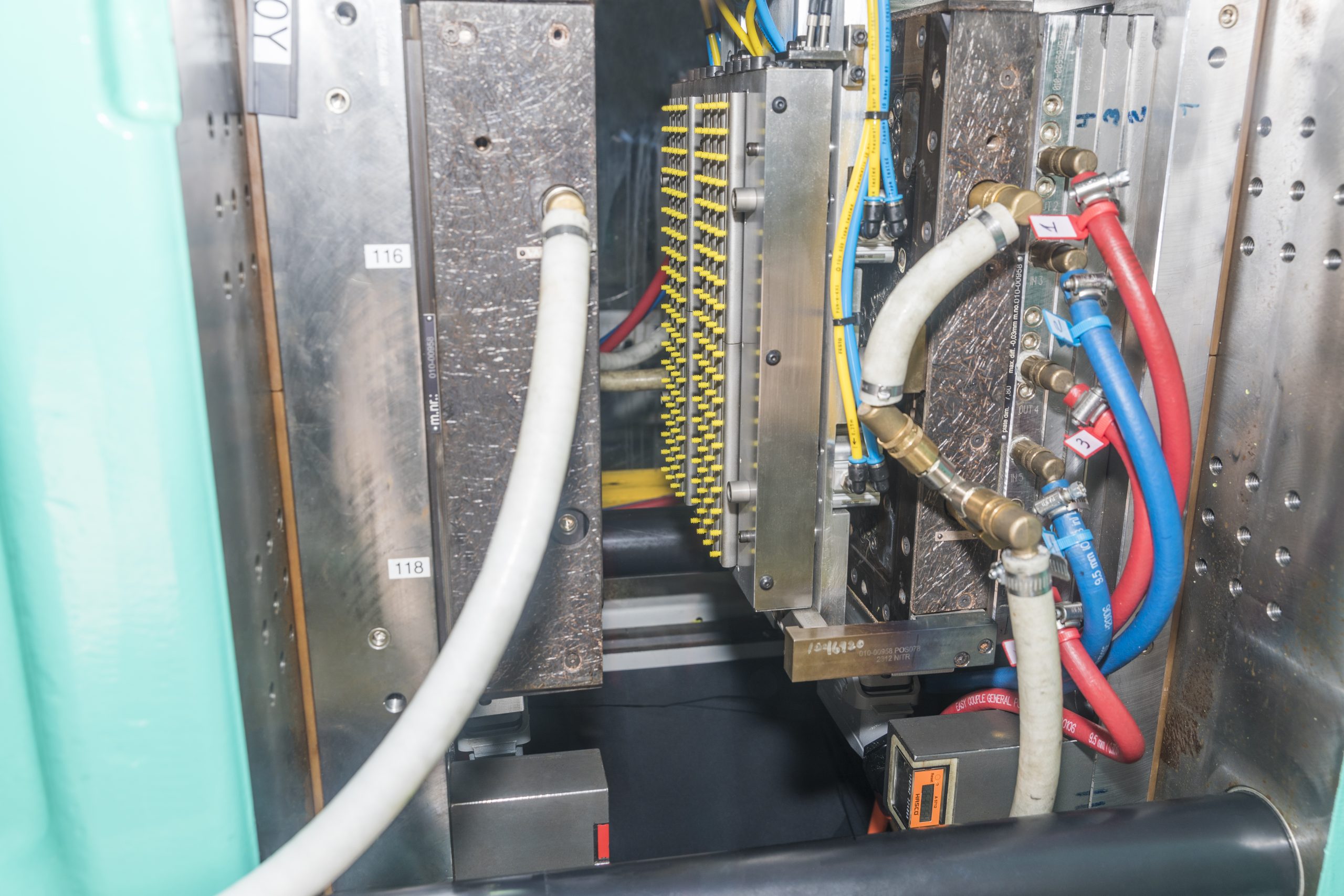
SIMTEC has been producing precision Liquid Silicone Rubber (LSR) parts and LSR multi-material components using advanced liquid injection molding technology since 2002. We have a long history of providing value-added, turnkey LSR solutions for our customers in the medical, automotive, industrial, and consumer industries.
Our technology-driven facility consists of fully-automated liquid injection molding cells featuring premium molds, advanced molding technology, automated parts handling robotics, a class 8 clean room for hygienic production requirements, and inline post-molding stations for value-added processes.
Benefits of LSR for Your Project
LSR’s thermal, physical, and chemical characteristics make an ideal choice for your products if performance, longevity, and quality are valued necessities. We source materials from the leading LSR material suppliers, so you can trust the material’s integrity and availability. In addition to visual and dimensional inspections and functional parts testing, SIMTEC’s inhouse metrology lab can also perform material testing.
When you choose SIMTEC as your source for Liquid Silicone Rubber parts, you gain a reliable partner with decades of LSR knowledge and experience. LSR materials offer exceptional benefits that will further enhance your product’s performance:
Biocompatible
Medical and healthcare product manufacturers have embraced LSR as their first choice for products that have contact with the body, due to LSR’s compatibility with human tissue and bodily fluids, and its ability to withstand sterilization. LSR is also a ideal for skin-contact consumer goods, and medical and healthcare devices due to its biocompatibility, soft touch, resistance to bacteria and tolerance to cleaning products.
Hypoallergenic
LSR is a preferred material in the life sciences and mother and baby care industries for products in contact with users’ bodies. Unlike latex and other materials, LSR will not irritate sensitive skin and does not cause allergic reactions.
Tasteless and Odorless
Liquid silicone rubber is widely used in food and beverage products because it is tasteless and odorless. LSR also complies with the Food and Drug Administration (FDA) regulations and standards, an important criteria for baby products, respiratory masks, and products used in the preparation, storage and dispensing of foods and beverages.
Durable
Parts made with LSR can withstand harsh conditions, extreme heat and cold, exposure to UV and a variety of other harsh chemicals and fluids. Liquid silicone rubbers also have a high compression set allowing products to return to their original shape when subjected to multiple compressions, even in extreme temperatures. LSR is also ideal for the automotive / mobility industry and can be found throughout the vehicle – in interiors, exteriors and under-the-hood. It is also suitable for products used in outdoor applications and other harsh environments.
Industries and Applications
No matter the industry, SIMTEC’s liquid injection molding cells produce LSR and LSR 2k parts that can withstand harsh conditions and repeated use, adding value and resilience to your products. SIMTEC produces hundreds of millions of parts each year for a wide range of products in a variety of industries:
- Automotive: In the automotive industry, we manufacture custom LSR components used throughout vehicles. Connector seals and grommets used in electrical systems, sensor components providing safety to drivers and their surroundings, key fob and keypad membranes, vibration inhibiting cushions, battery seals and components used in HVAC systems.
- Life sciences: In the healthcare and medical industry, Liquid Silicone Rubber is used extensively. High-volume seals, gaskets, valves and diaphragms; actuators and sleeves used in surgical devices and equipment; septum, cannula, and plugs used in drug delivery products as well as a range of other performance-critical medical components. Healthcare products such as wearable glucose monitoring (CGM) and other healthcare monitoring devices, respiratory and CPAP masks, and hearing aids and ear protection products among others.
- Industrial and special applications: Regulating valves and thin delicate LSR membranes and diaphragms are used in gas water heaters and furnaces to sense the slightest variation in gas and air flow. Seals and covers are used in safety products like smoke and CO2 detectors and other safety products operating in harsh industrial environments.
- Consumer products: Sanitary kitchen and bathroom products such as appliances, plumbing, and personal hygiene products, as well as consumer electronics have discovered the advantages LSR offers. LSR seals, gaskets, sealed housings, and diffusers, spray faces and caps used in faucets, showerheads, and toilets. In consumer audio products, LSR components are found in sound resonating passive radiators in speakers and flexible ear tips for ear buds and headphones.
Why Work With Us for LSR Injection Molding Capabilities
Since our inception over two decades ago, we have produced billions of custom parts for our business partners. We continuously expand our technology and build-upon our expertise to deliver accurate, reliable, superior quality, high-volume LSR components. Our technology, value-added services and molding expertise offer advantages that give our customers an edge over their competition. Some of these value-added benefits include:
Molds and Automation Made for Continuous Production
Our class 101 LSR production molds and parts handling automation are designed and built for long-term, hands-free production. They are finely tuned to pair seamlessly with our advanced molding technology for optimized manufacturing, maximized productivity and high-yield production.
Innovative Molding Technology and Quality Assurance
Our innovative technology and precision LSR, LSR 2-shot, LSR overmolding, and LSR multi-shot molding processes are optimized for efficiency, productivity and quality. We are ISO 9001, ISO 13485, and IATF 16949 certified and have maintained these certifications for many years. Our state of the art quality metrology lab, upfront quality planning and dedicated project management ensure streamlined operations and allow us to deliver the highest quality parts, consistently.
Value-Added Operations
We take a total system approach, planning, integrating and automating post-molding operations. Performed within the manufacturing cells, secondary processes take place immediately following demolding. Each custom-designed process is robotically performed with precision accuracy to enhance quality and streamline the total manufacturing process shortening our customer’s supply chain and adding value.
Production of a Wide Range of Part Geometries
We combine the advantages of LSR and LSR liquid injection molding technology to produce a wide range of part configurations, from simple to complex, tiny to small, in one LSR material or multiple materials. Our understanding of LSRs and our advanced liquid injection molding expertise have set us apart and established SIMTEC as a leader in the industry.
Industries and Applications
Regardless of the industry, our liquid injection molding cells allow for the production of liquid silicone rubber parts or components that must withstand extreme conditions and make your products more effective. Industries and applications include:
Get Started with Custom LSR Solutions
SIMTEC’s unwavering objective is to produce high quality custom LSR injection molded parts that will satisfy our customers needs and offer advantages for their products.
Contact our office for information about how we can manufacture your product.
Contact SIMTEC To Discuss Your Project Today
With design flexibility, advanced technology and exceptional quality, there’s no better partner to manufacture your high volume Liquid Silicone components than SIMTEC. Contact us today to discuss your requirements.